|
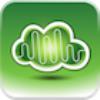 Australia | It is a new concept so it is not a stupid question.
Virtual Wrench was created by Leica to solve the biggest problems associated with servicing high tech ag gear.
1) Unnecessary Service - In the past, simple user problems could cause the dealer to send out a service technician when it wasn't really needed. The Tech would fix the problem or train the user and have to charge for the trip. Sometimes they couldn't charge for the trip. Sometimes the tech swapped everything out and hoped for the best. Either way it was costly for the farmer and the Dealer. Virtual Wrench means the Dealer can diagnose problems remotely before a decision is made to send out the Tech. This saves everyone money, and if the tech does have to go out then they should have the right parts to fix the problem and not need to run back to town and drive out again. We are finding most service visits can be avoided by using Virtual Wrench.
2) Wrong Diagnosis - Trying to diagnose over the phone generally involves conversations like "what do you see on the screen now... you shouldn't be seeing that?... try pressing this button now and tell me what you see." The farmer and the tech are playing phone charades and it generally ends up in wasted time and money. Leica dealers can dial directly into the mojoRTK autosteer and view what the farmer sees on the screen. The tech can push buttons, tune the steering, look directly at error logs, and watch the performance stats of the steering live on the screen. This improves problem resolution times and reduces costs for the farmer and dealer.
3) Reduces Downtime - Virtual wrench means that the Dealer can get to the equipment in the time it takes the farmer to press the request for service button on the mojoRTK unit. This is a lot quicker than a service truck takes to drive out to most farms. During critical periods, time is money of course, and in those same periods the Dealer's service tech's are at their busiest and may not be able to get to you in the same day. Now they can.
4) Software Upgrades - I think many autosteer and other ag tech users have experienced the "upgrade gone wrong" scenario. That is, the service tech drives out, you get the latest and greatest software upgrade for your gear, the service tech leaves... and the upgrade doesn't work or has bugs that stop you working. You call the tech back and he says "that should not be happening?" You are left waiting for the tech to come back out and get you back to the old version while the problems are fixed - more driving. With Virtual Wrench, we upgrade you in 20 mins or less over the cell data network, if there are problems we can roll you back to the old software version with the press of a button. Every mojoRTK stores the old software onboard as well as the new for this reason.
5) Training - Virtual Wrench enables Leica staff or Dealer staff to train farmers on the system remotely. We can show you how to tune the autosteer, walk you through setup, or any other function of the system. All this without paying for a service truck visit.
Note also, that neither the dealer or Leica can access your system without you pressing the 'request for service' button. This is for privacy reasons. After you press the button, your request will be dealt with in order according to your service agreement terms. The tech will access your system and review the error logs and performance stats BEFORE he calls you. When the tech calls your cell phone, hopefully they will already have some answers.
Hope this helps
John | |
|