|
|
NE ND | Wanted to get some opinions on grain bin forms. Looking to move s couple 21' 7000 by bins and trying to do most everything ourselves to save money. Gonna do 18" footer and called local shop to make forms. 1/8" steel 18" tall and 10' long. They're gonna put 90 degree bends in each end and drill holes so I can bolt em together. Was gonna weld some square tubing on myself to put rerod stakes thru. 1200 bucks they quoted me. Plus I'd have s little more into stake pockets. This is for 14 sheets, enough to do 2 bins at ounce. Think it's worth it? I thought about using lap siding cause it would be cheaper but I can only get 12 inches tall. Plywood sounds like it sucks. I could get half as many but then have to do the project and pour twice. Also with more sheets I could do larger bins in the future. Any thoughts/opinions? |
|
|
|
| For that size bins, I would use plywood. The cost is minimal, and easy to tie
together. |
|
|
|
west central ohio | Have used the same style but had pipe instead of tube steel. They had nuts welded to the pipe and used rebar for stakes then ran bolt through to set grade. I would go 24" tall...mine is 18" and cheated it a bit and still fight to get swing away auger under it. Enough to do one bin at a time..30 yards would be enough for me and only $600.00
Edited by alfalfa338 6/21/2017 09:03
|
|
|
|
Huntley Montana | Just find another bin, cut the bottom sheets in 1/2, add 1/2 a sheet to the ring, & you have forms. |
|
|
|
Southern NJ | This is what I would do if I had to do another one. We used lumber and made the pad an octagon. Using old bin sheets would be the ticket. |
|
|
|
NE ND | I get the ring idea, but I'd don't really have to time to find another bin. Trying to get these things up by pea harvest and that's about a month away. |
|
|
|
NC ia | Do you plan on doing more in the future? If you don't I would use ply wood use 2x4 for your stakes and hold the seams together with 2x6s. Quick easy and cheap |
|
|
|
CIL | I can take pictures of mine and send them to you if you text me ThreeZeroNine2SevenFive5ZeroZeroSeven |
|
|
|
live in Spfd, farm located NW Macoupin county | One of your statements has me concerned "enough to do 2 bins at once".. Trying to do 2 pads at the same time could be a real challenge. |
|
|
|
Western Iowa | I have done several pads that size over the years. Just rip some 3/8 plywood down to the width you want (18"). Pound in a 2x4 about 12" into the ground at each 8ft seam and screw the plywood to it. Pound some chunks of rod or old steel posts in between the 2x4. Then take a log chain and wrap around the whole darn thing with a few load binders. Will need to spike in a few 16 penny nails to help hold the chain up until its tight.
It works, it holds fine, pretty fast, and its cheap.
I would recommend just going with 24" though. Never regret a little more clearance on auger and keeping the bin up out of dirt and grass. A few yards of sand is cheap in the scheme of things to add the 6". |
|
|
|
SE Nebraska | Agree. It seems logical. But you will be dead beat after number 1 and 2 will be out of the question. Unless you are way overstaffed with people. And even at that time will be against you to get screeding and trowling all done |
|
|
|
NE ND | I get what you guys are saying about being tired after one. But wouldn't I still want to have the forms set up for both at the same time? Could pour one and then do the other the next day..... |
|
|
|
KS/ NENE | We used a set of borrowed steel forms to do our bin last fall, they do work nice. I would set and do only one at a time, you can strip the forms after 2 days any way, and it won't take long to set up the second one after you have done the first. Pour on Monday, strip Wed morning, pour in the afternoon, bins could be set the following week. |
|
|
|
Eastern Kansas | Here is the forms from our 42' |
|
|
|
SWMN | Seems kind of steep considering 5x10 sheets of 10 ga can be bought for under $110 ea and each one will make 3 20" x 10' forms, their cost is around $520 material + 680 labor. I would consider using 12ga 5'x10' sheets, cutting them in thirds with a plasma cutter by using an angle iron as a guide, welding 1-1/4 x 1-1/4 x 3/16 angle angle irons to end of sheet for splicing and getting by for under $500. I would probably take the better part of a day to build them. |
|
|
|
| Nodak63 - 6/21/2017 07:50
Wanted to get some opinions on grain bin forms. Looking to move s couple 21' 7000 by bins and trying to do most everything ourselves to save money. Gonna do 18" footer and called local shop to make forms. 1/8" steel 18" tall and 10' long. They're gonna put 90 degree bends in each end and drill holes so I can bolt em together. Was gonna weld some square tubing on myself to put rerod stakes thru. 1200 bucks they quoted me. Plus I'd have s little more into stake pockets. This is for 14 sheets, enough to do 2 bins at ounce. Think it's worth it? I thought about using lap siding cause it would be cheaper but I can only get 12 inches tall. Plywood sounds like it sucks. I could get half as many but then have to do the project and pour twice. Also with more sheets I could do larger bins in the future. Any thoughts/opinions?
Why bother with the 90 degree bends , lap them together with a 4" splice and bolt them together. |
|
|
|
45 miles south spingfield il. | I use Masonite siding 12 inch wide rip into two six inch pieces. Drive wooden stakes in ground, they just are to keep form level. Then I backfill with sand dirt or rock . I put a rod in middle of site set 2x4 with pipe on rod when the 2x4 is level screw siding to wooden stakes, go on around forms. I don't take forms off but you could. |
|
|
|
NW Iowa | Guys that do it every day get by with plywood
(IMG_0317.JPG)
(IMG_0323.JPG)
Attachments ----------------
IMG_0317.JPG (134KB - 78 downloads)
IMG_0323.JPG (222KB - 53 downloads)
|
|
|
|
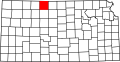 Northcentral Kansas | We have always used Masonite siding. We pile dirt dug out of the footings against it. |
|
|
|
western iowa | I've done 21' and 24' pads for bins using 3/8 plywood. I figure out what diameter I want the pad then figure the distance around. I overlap the plywood and put 3 bolts in each joint with the nuts out for taking them off. I pre-drill the holes before putting it together Put the stakes wherever you want them and put the dirt from the footing on the outside of the plywood to help support it. |
|
|
|
just a tish NE of central ND | Beg or borrow some forms from somene .......or RENT THEM........Steel forms............ Wood works but turns into more labor and you throw them away. I WILL never use siding for a bin again as you need lots of stakes and reinforcement and hand pile dirt agaisnt them and the darn things are flimsey and not wide enough so you HAVE TO DOUBLE THEM TO GO DEEPER........ and that kind of work is time consuming, hard on the back and you still wonder if they are going to burst with the forms full and a truck waiting to finish pouring it in.
STEEL FORMS> |
|
|
|
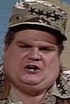 Mather, Manitoba | I see your handle you maybe located in North Dakota. Can rent steel forms from Killarney Farm Supply in Killarney Manitoba. If you buy from them, they'd be free to use. Steel 12", 18" and 24" forms. |
|
|
|
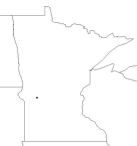 Benson, MN | Don't weld the square tubing directly to the side of the form. weld 2" or 3" flat bar set on edge to the form and your tubing to that. Gets your pocket out away from the form so when you pound in your stakes your less likely to hit the top edge of the form. |
|
|
|
Central Wi | Just use the sheels from your bin. Should be a half sheet by door or just use an extra full sheet. Spray with deisel fuel with a hand sprayer right before you pour it. Did 2 here like that. The little concrete stuck to sheets will wear off in a couple years. $1200 is a waste of money. |
|
|
|
EC North Dakota | Use steel. Either rent or buy. Don't cheap out, you'll enjoy having your own steel forms if you're going to do more in the future.
Don't use wood or a bin ring.
Go 24" high. |
|
|
|
Kingston,Mi | I would rent the 2 x2 ft. steel and plywood commercial forms, 34 pieces for each bin will provide a 21.6 ft. diameter pad. As some one said form, pour, strip in 2 days in the morning then form the other pad, pour and strip then call the rental and have them picked up. Then you don't have to try and find a use for a truck load of junk plywood. A contractor on a job I was the inspector on called for a specific bundle of forms, the rental/concrete supply company brought all the forms, keepers, ties, strong backs, turn buckles and a pile of other consumables. His crew set 2 walls, poured them, stripped 2 days later and piled the returnables. About a month later he was ready for the second set of walls and the forms came back. He had something like 300 carpenter/millwrights working for his firm and didn't own any forms. Even tapered wing walls were done with rented forms, just added a shaped chine to the assemble forms to define the top of the wall and form a good edge.
Edited by BOGTROTTER 6/21/2017 14:54
|
|
|
|
South Central MN | I have steel bin forms I would sell! My email is good. |
|
|
|
| Dad used plywood for the 4 he has poured. Run a couple of cables around them. Think we used 3 bolts per seam. Slick and cheap.
AaronSEIA |
|
|
|
WCIL | That's what we do. Pound a pipe in the center to grade, put a long bolt edge wise in a 2x6 for a pivot, then set the board on the grade pipe and level plywood forms to that. When pouring have some helpers inside with rakes and a guy striking the cement with the 2x6. We "chop" the board up and down a little to "float" the top. No bull floats here. Not hard at all. Done 18' to 36' this way. Cheap and effective. |
|
|
|
 Ludington/Manistee MI area | Good heavens folks can make something simple complicated!!!
4X8 sheet of steel not sure on gauge I'm not a fab guy ripped lengthwise. Weld a 1.5 inch angle on the end to make a flange to bolt pieces together with matching bolt holes on each. Two pieces of tubing tacked to it set screws to set height. We hired our first pad poured and watched the crew this is what they used so we leveraged the idea. The difference in us doing the next pour ourselves paid for the forms and our time. The next 7 pours we profited on. |
|
|
|
| 2 days? I'm stripping forms in 4 hours. |
|
|
|
west central Iowa | We put up two 24' bins a few years ago. We just went with 12" forms and dug down another foot on the I side for rat barrier. Did rented steel forms on one and siding on the other. I preferred the siding. We didn't use cable or pile dirt on the outside and had no problems. |
|
|
|
Glasgow, Ky | +1 on the masonite. Done several like this. Cheap and works great.
Anything more is a waste of money. |
|
|
|
KS/ NENE | All depends on your mix, ambient temps, humidity, thickness, etc. If you are running some accelerator and temps are favorable, sure. Look at a slip pour, they uncover fresh concrete out of the form every 4-5 hours and it has to hold everything on top of it yet, but 2 days is a safe bet no matter what you are doing and a good rule of thumb for DIY concrete. |
|
|