|
|
Central ND | When the run a little too fast? I have always wondered why they look triangle. Why not just oblong or oversized. How can this be prevented in thin sheet metal?
Just wondering. |
|
|
|
NW Iowa | I always thought it was because the point of the bit is through the metal before the entire cutting edges are entirely into the hole. The point gives the bit stability but it can't give stability if it isn't anchored. I might be all wet on this one. Hopefully a machinist will set us straight. I use a stepped bit in tin, the hole ends up close to being round and it doesn't grab as bad. |
|
|
|
Middlesex County, Ontario | Brother is a sheet metal worker. Use a unibit or a sheet metal drill.
Here's how to grind a sheet metal drill profile.
http://qrpbuilder.com/downloads/sheet%20metal%20drills%20a.pdf |
|
|
|
Wi | Because the bit wants to dance around the hole. The centering point helps on thicker stuff but on thinner stuff it's through the piece quickly. |
|
|
|
w/c Illinois | I seem to recall from high school metal shop class that a twist bit never makes a perfectly round hole in any thickness of metal. If you want a near perfect hole you have to use a reamer. |
|
|
|
| This is true. In high school shop class the teacher had some picture of two holes, one done with a good sharp drill bit and one done with a reamer, and under a microscope of something the drilled hole wasn't round and was jagged and rough as could be. Reamed hole was perfectly round and smooth.
As far as sheet metal goes, I have a couple of step drills that work nicely on it. Hate drilling sheet metal with a regular drill bit. |
|
|
|
United States | with thin sheet metal is it distorting the metal as it goes through? (not a flat plain) |
|
|
|
South Central Illinois | Clamping the sheet metal to something thicker will help. |
|
|
|
michigan | I am a tool and die maker by trade and there are special ground drill bits for sheet metal, they have a undersize point on them for a pilot and then cut the the full diameter with a an end that is similar to an end mill. Another option is a step drill or some manufactures call it a uni-bit. |
|
|
|
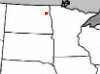 NEND | I agree that the hole isn't round because the web/chisel point of the drill has to keep the drill bit in control and starts wondering around. Your original question is why is it triangle shaped, and no one has answered that part of the question. I have wondered why this is as well. You have two flutes on the drill bit, how does it wobble around and make a three-sided hole. I'm not sure frankly. There have been good solutions mentioned. I have a uni-bit that works well. If you don't have one of those, step up to the desired size gradually with regular bits. |
|
|
|
| this is quite simply because a drill bit uses 2 flutes. even in thick metal, if the bit is sharpened even the slightest off center, the bit will always drill a triangle shaped hole. it is because the outside edge of the long cutting edge will grab the metal at the edge of the hole and "walk" the short cutting edge around until it touches the outside edge of the hole, and so on. An uneven bit used like this for any amount of time will eventually break off where the flutes meet the shank from working back and forth.
on sheet metal, as has been said above, the web of the bit has no anchor, and for an amount of time the cutting edge is unsupported except for downward pressure, allowing the corners of the bit to dig in and walk the cutting edges around. |
|
|
|
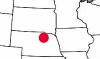
| its because the sheet is grabbed at the last millisecond, and PULLED up the bit, and leaves the torn part that resembles a triangle. Support both sides, TIGHTLY... with blocks of wood both sides. |
|
|
|
SESD | Wankel (rotary) engine effect. https://www.google.com/url?sa=t&rct=j&q=&esrc=s&source=video&cd=2&ca... |
|
|
|

| A unibit works but the best solution is a hole punch. I have several. I've had a Whitney Jensen #5 jr for about 50 years and there are Asian knockoffs on the market today. I've had a Whitney Jensen #15 for several decades. The punch has a point, just feel it into the center punch mark and squeeze the handles, a hole takes a second or less and is round. The #5 does 1/16 to 9/32. The 15 has a bigger opening and does small to 17/32" I have a couple others that do up to half an inch in 1/8 or thicker steel, not just thin sheetmetal. The little punches do fine in 1/16" steel and aluminum. There are shop sized turret punches that do a wide variety of hole sizes but are a lot more costly than the little ones I have.
135 degree split point bits should do better in thin sheetmetal than standard bits because they cut to the center while the standard bit doesn't. Last week Menards had a special on a kit of 135 degrees split point bits, 160 of them from 3/64 to 1/2" for $15 after the rebate. I haven't tested them yet.
Gerald J. |
|
|
|
Middlesex County, Ontario | School Of Hard Knock - 12/15/2015 23:18
I have always wondered why they look triangle.
Just wondering.
The bit wants to walk in the hole because the edges of the bit grab. We can all imagine and agree with that I think.
Imagine the 2 corners of the bit basically form a straight line. Imagine a square. Your line (bit) is one one of the edges of the square. As you rotate your line (bit) the line will eventually lay on a different edge of the square. This cycle repeats as the line rotates. To visualize it look at square hole drilling videos, wankel videos, etc. Like other people are saying. If you've seen a planetary gear set in action; your bit is kind of like a planet gear and your hole is the ring gear.
This works for any shape. So why does the hole end up being a triangle? Well what shape has the least amount of sides?
Its maybe hard to explain in words. Basically its going to favour a shape with less sides, and there is no shape with less sides than a triangle.
Edited by WildBuckwheat 12/16/2015 12:29
|
|
|