|
|

| I have some 1" plate and some 4"x6"x 1/4". The 1" plate will be laying flat and the 4x6 will be setting vertically on top of it (one open end of the tube will be covered by the plate).
My understanding is that if you weld these two pieces together, the 1" plate will cool down very fast after you're done welding and weaken the weld. To prevent this you should pre-heat the 1" stuff. How hot should I get it. I can measure the temp with an infra-red gun. Thanks. |
|
|
|
68340 | I would just bring it up to cherry color. Get my torch shut off and laid aside. Get the 4 x 6 in position. Weld it up all around 360 degrees. Relight the torch and keep it warm so it does not cool off to fast. Gradually removing heat.
Are you grinding back the edge of the sq. tube before you weld? A true good weld should penetrate all the way to the inside of the sq. tube. This can be accomplished by the grinding back and/or by have a washer under the sq. tube to give you a 1/16 to 1/8 inch space between the sq. tube and the flat iron.
You will need a slightly lower amp setting on the welder because of the hotter flat iron. I know when I preheat cast before I weld I need to turn the welder down any where from 20 to 40 amps or else I burn all the metal away.
I do not know of any mfg. that goes to all the trouble I have written above. You must be putting a great deal of strain on the 4 x 6 to require such a weld. Yes ? |
|
|
|

| It is way overbuilt for what it is, but I really don't want it coming off while going down the road. It's for mounting some J.D. Skiles volumetric cylinders on the side of a spray trailer. It will be gusseted as well and will normally not weigh much more than 1000 pounds between 5 cylinders and the bracket but if we get in a bind and have to head home while one or more are full, I don't want any problems.
Thanks for your suggestions. |
|
|
|

| For what it's worth, I'm also intending to use my wire welder. MM252 with .035 wire. |
|
|
|
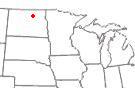
| 24 volts, 475 wire speed. Weld away you will have no trouble as long as you are a decent welder. |
|
|
|
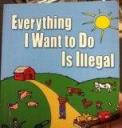 Whiskey, Tango, Foxtrot | Without knowing your exact alloy, it is hard to know for sure. Most preheat reccomendations are not that hot, 250-450* F.
There are crayons you can buy to stick the steel with, that melt or change colors at different temperatures. Probably not neccessary for most applications however. Guy I worked with who was a very good welder thought too much heating (actually the rapid cooling afterwards) was worse than not enough. Usually if a heavy plate was hot enough to make spit sizzle (200*F) where we were welding to it, that was hot enough. Wrap or keep a little heat to cool slowly is as important. Most of the stuff we maintained was on rock crushers subject to extreme vibration, stuff breaking off was fairly common so you learned quickly by experience was works and what doesn't. |
|
|
|
Leeds, North Dakota | Daniel, 1/4 " to 1" is gonna be difficult, what I would suggest, try a piece of scrap first, use carbon dioxide, spatters terrible, but better penetration, I am a miller man,I don't think your welder is gonna cut the mustard, I think you would be better taking to a welding shop with a production welder. What concerns be is the big difference in materials, preheat, next to impossible, we have a production welder 3 phase wire speed 700 rpm drawing 250 amps, one inch gets so darn hot, penetration unbelievable, good luck, Scott. |
|
|
|
Western Iowa | x2
Don't heat it cherry red. The 'spit' test is a good farm rule of thumb. If you need to pre-heat you need to let it cool slowly as well. |
|
|
|
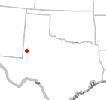 West Texas | You are joking right?
I mean, wow, there must be lotta stuff around here that must be about to fall apart then. |
|
|
|

| Thanks for the help everyone. We were already done before we got some of the suggestions.
We ended up running the welder at 26 volts and 475 on the wire speed. I did grind a bevel on the 4x6. We heated the plate up to around 200 degrees. I can't imagine how long it would have taken to get it cherry red as I do not have a rosebud so I was using my biggest cutting tip. We had two plates that needed to be welded so we heated one for awhile, then the other and kept switching back and forth hopefully giving the heat time to evenly spread through the whole plate.
Next I welded all the way around each 4x6 and then made a second pass on the lower side of the first weld and then made a third pass slightly higher than the first weld. It's been long enough since high school welding class that I don't know what that process is called but it looks like this fillet weld (maybe not quite that smooth). Is a fillet weld only a fillet weld when it's a T like that or is it still called a fillet weld when you're using tubing?
Anyway, I did not put a torch to it to let it cool down more slowly. Hopefully that won't hurt it too much. For as much as it's overbuilt, I can't imagine it being a problem, but I guess I'll know more in 10 years or less. The steel was 50 degrees before we started preheating so surely it's better off than it would have been.
Thanks for the help everyone. |
|
|
|
northwestern middle tn | If it is just carbon steel I wouldn't worry about the preheat, you
will have it up to heat after the first couple of rods. If you are
determined to preheat 200-250 degrees is what the preheat is
on it. If I understand what you are wanting to do correctly,
you need about a 1/2" fillet weld around the tubing to the plate.
I like stick rods better than wire feed, 7018 is what I would use.
Pre heat is more important when dealing with metal with chrome
in it.
You figured it out while I was typing!
Edited by CumberlandFarms 1/11/2013 20:11
|
|
|
|

| Haha, thanks for your comments anyway, makes me feel better about what I did. |
|
|
|
northwestern middle tn | You did it the proper way. A fillet weld doesn't have to be in
the classic t shape they show in all the books. |
|
|
|
| I would have welded as you did but no pre heat. I hold the rod on the first pass closer to the heavy steel.I have used my propane space heater to pre heat aluminum. It is easy to heat a large area fairly quickly with one. Also not a sharp temperature change at the edge of your heat like with a torch. |
|
|
|
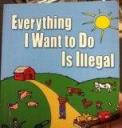 Whiskey, Tango, Foxtrot | I agree with Dutch, there is nothing complex or secret about that weld. Actually, in my shop, welding 1/4 tube to 1" plate is pretty common. I like 1" plate to make cylinder mounts. A common mistake is not getting good heat and therefore penetration into the heavier plate. Preheating can work, notching can work, welding it hot and focusing on the heavier plate can work, multipasses can work, or just grab some 7018 and stick weld it if your that worried about it. But it isn't uncommon or something that needs a production machine. |
|
|
|
 central ILL | Do you think in a factory they preheat everything like that before they weld it. Weld it and be done with it. |
|
|
|
Leeds, North Dakota | Maarten, just a obersvation, didn't say it wouldn't work, I work in a machine shop so we have welders farmers don't have, sorry if I was understanded wrong, thats why I said carbon dioxide, with different thickness material. Your welds will be fine with gussets, you will not have any issues, a couple posts have stated when mfg's weld, first off they use production welders, its the most efficent way, normally metal thickness is close to the same, Scott. |
|
|