|
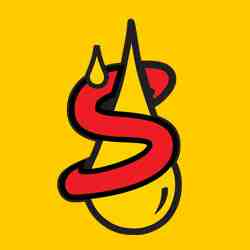 Seaford, Delaware |
Filtering Out The Facts
One of the methods all diesel engine manufacturers have adopted to reduce emissions - especially particulates - is to drive fuel injection pressures way up and force the fuel through ever-finer injector holes, typically so small they are drilled with lasers. This extremely high pressure - 30,000 psi or more - and precise injection spray patterns force the fuel into tiny droplets, increasing the surface area of the fuel in each injection event and maximizing its chances of combustion.
The problem is that any dirt or moisture in the fuel will wear the fine clearances in the injector pumps and erode the carefully machined holes in the injectors, leading to a reduction in performance, a rise in fuel use and poor emissions control.
These consequences take time to appear, but there is plenty of evidence to show that time and poor fuel husbandry will show up as damaged injectors.
To make sensitive injection parts in modern diesels last as long as possible, engine manufacturers require fine filtration of the fuel as it reaches the engine, usually two-stage or even three-stage filtering.
Unfortunately, fuel seems to be increasingly dirty, more abrasive and contaminated with water. So it's an almost certain bet that during any meeting of the Technology and Maintenance Council some manager will ask about fuel filter plugging.
In order to gain any sort of life for the fuel filters in this much dirtier fuel environment, engine manufacturers have set the media size for secondary filters to address particle size down to 5 microns at the most extreme. Some, like Cummins, only require a 15-micron secondary filter. This makes filtration less of a maintenance issue, but it doesn't block a whole lot of the 5- to 10-micron particles that can be the most abrasive.
And it's not limited to big-bore trucking diesels. At a GM Dura Max forum, there is some suggestion among users and repairers that a 2-micron filter is necessary to really protect the injectors in those engines.
But if truckers are finding 15-micron filters plugging at unacceptable mileages, are they likely to switch to a media that'll plug up even sooner? The temptation is to go to a wider spec on the filter media. That may reduce filter plugging, but will allow more harmful contaminants into the engine.
One possibility is to try using a different filter of the rating required by the engine maker. All filters are not the same. Some have a greater area of folded media and can absorb more dirt and goo before they choke off the fuel flow.
Before It Goes Into The Truck
The real solution, though, is good fuel housekeeping. Fuel should be purchased from a reliable source and stored in tanks that are not old, rusty or contaminated with dirt or water.
The fuel from the refinery should have been filtered down to 30 microns (and pumps at fuel islands should also have 30-micron filters). It makes sense to filter fuel stored in your own tanks with a finer filter as it is pumped into trucks. If those filters choke up, at least they can be changed without a load being stranded at the side of the road.
Also, these filters will give you a clue about what is blocking the secondary filters out on the highway. You can test to see whether it is a biological contaminant or a degraded fuel with dropped-out asphaltenes. Armed with this knowledge, you will be able to treat with a biocide or do something about your fuel supplier and his handling of the fuel.
First, though, the fleet must test the diesel fuel source to find out exactly what it is purchasing. Diesel fuel is the trucking industry's No. 1 commodity cost of operation. Yet very few companies regularly test their diesel fuel quality. The fuel tests should be for cetane index plus ISO cleanliness code.
Poorly maintained storage tanks can also contain significant amounts of water, which results in microbe and algae growth that can cause fuel filter clogging. The acidic by-products of microbe life causes tank inner wall corrosion, further increasing fine fuel contaminants.
Many tanks have a poorly designed vent system with a wide screen that is able to keep little more than bricks and birds out of the tank. It is very important to think about this point of entry for dust and other contaminants.
Once fuel quality and contamination are determined, a plan can be implemented to reduce contaminant levels.
Acknowledging the problem of injector erosion, Detroit Diesel offers a tune-up kit for the Series 60 under the Power Pack name. A small brochure for the kit features electron micrographs of typical injector tip hole erosion. It recommends replacing all six injectors when the rocker cover is removed for a single bad injector, because the time taken is only two hours more to restore power and performance. Detroit endorses the use of the Davco Fuel Pro 382 fuel filter/water separator and recommends it be installed at the same time as injectors are replaced.
ULSD Problems?
There is concern that the ultra-low sulfur diesel introduced late in 2006 is responsible for some of the fuel issues being seen in trucks and in refueling equipment.
"We are really concerned about this problem becoming more widespread. If this is a corrosion problem that occurs over time, what we are finding now could be the tip of the iceberg," says Holly Alfano, vice president with the truck stop association NATSO. It and the Petroleum Equipment Institute are supposed to meet with EPA underground tank officials to discuss what can be done.
Corrosion of steel fuel tanks on the truck has become an issue with Ford Super Duty and F-Series trucks. According to a Georgia-based service manager, the tanks are on back order as so many replacements have been necessary.
The corrosion incidents are among a number reported to a subcommittee of the American Society for Testing Materials by the Steel Tank Institute.
Trouble with ULSD in diesel engines is not new. When sulfur was reduced to 15 parts per million in ULSD, to counter concerns about loss of lubricity, refiners began mixing in lubricity additives to ease the problem.
But the answer is not easy to find, according to Lorri Grainawi, technical services chief for the Steel Tank Institute. While the damage appears to be widespread, there are no obvious patterns, and damage reports are coming from stations old and new, from high- and low-volume locations.
NATSO surveyed its members and found that 42 percent have experienced equipment problems since ULSD was introduced. The survey was in response to reports of increased corrosion in both steel and fiberglass tank systems.
But while there is a considerable body of anecdotal evidence of the corrosiveness of ULSD, a stakeholders group that includes the U.S. Environmental Protection Agency, American Petroleum Institute, NATSO, Petroleum Equipment Institute, Petroleum Marketers Association of America, National Association of Convenience Stores, Society of Independent Gasoline Marketers of America, American Trucking Associations and others have recommended no further research into the perceived problem.
As well as the corrosion caused by water in the fuel - which does seem to be a phenomenon associated with ULSD - the interface between the diesel fuel and any water that separates out is the breeding ground for microbial action that can accelerate corrosion from the production of sulfuric acid. But while the corrosion is a concern for the steel tank people, it is the microbes themselves that cause truckers such heartburn. That sticky goo that is blocking up fuel filters is often the bio material that is growing in diesel fuel tanks.
The microbes live at the interface because the water brings oxygen for them to survive. So there is a two step-process to eliminate this contamination: cutting out the water and treating the tank with a diesel biocide.
However, says John Nightingale of Dieselcraft, the bacterial contamination and the presence of asphaltenes are commonly confused. The asphaltene sludge can be mistaken for bacterial contamination, but it obviously will not be eliminated by a biocide. Accordingly, says Nightingale, if you're experiencing filter plugging, you should test to see what is causing the problem. To that end, Dieselcraft is offering a test kit that can be found at diesel parts stores.
With the Fuel Bug kit, the fuel is tested on a "lollipop stick" and cultured. If bacteria are present, growth will be apparent within 30 hours. After a little longer, mold or fungus can be seen.
Nightingale says there is a general lack of understanding and little concern for these problems, even though fuel condition can cause significant loss of performance, roadside service calls and long-term fuel pump and injector damage.
Making matters more confusing, biodiesel may be in the fuel you are purchasing whether you know it or not. States like Minnesota have mandated diesel sold in the state include a certain percentage of biodiesel, and that's what you're going to get. Other areas and blenders also add bio fuel to stretch the fossil fuel.
The first winter the Minnesota biodiesel mandate was in effect, there were a number of reported problems, which were traced to quality control issues. The American Society for Testing and Materials is the industry organization that defines legal fuel standards. In 2001, ASTM approved a standard specifically for biodiesel, ASTM D6751. However, notes the National Biodiesel Board, while ASTM D6751 ensures biodiesel quality, many distributors and fuel suppliers are unfamiliar with biodiesel handling practices. The board instituted a voluntary quality assurance program called BQ-9000. While ASTM standards only cover fuel quality, BQ-9000 encompasses storage, sampling, testing, blending, shipping, distribution, and fuel management practices.
What's In Your Fuel?
If you have your own fuel storage tanks and buy tank-truck loads, you have to make sure you know what's being delivered. Do this by taking fuel samples at the time fuel is dropped, marking the brand, the fuel carrier, time and date. Then store the samples for at least three delivery cycles and regularly check to see if any water has settled to the bottom of the bottles, or if the fuel itself is discolored or cloudy. If you have suspicions, send the sample to a lab for analysis. Then you may have to take action against the fuel provider and/or the delivery agent.
As recommended above, make sure fuel island dispensing pumps have functioning fuel filters - the lower micron rating you can use without seriously affecting the pumps' delivery rates, the better. Make sure these filters are changed at regular intervals. Stick the in-ground storage tanks with water-detecting paste or make sure your delivering trucker does. This procedure will give a heads-up to any in-tank contamination. And if any is found, have it chemically treated and/or pumped.
When are your vehicles fueled? Ideally, they should be filled at the end of day or run, because modern diesel engines - depending on make - recirculate as much as 90 percent of the fuel delivered to the engine. Each "trip" to the engine and back increases fuel temperature, and as the level falls, that in-tank temperature can reach well over 100 degrees. Hot fuel in a mostly empty tank leaves hot air, which cools and condenses, forming water droplets that are added to the fuel. That's why refueling before parking for the night or weekend is desirable. Also, the heating and returning increases the asphaltene deposits in the tank, and adding fuel will help dilute them.
Fuel tanks no longer have sumps -- the low point in the tank where dirt and water would collect. Sumps made it easier to drain off contaminants during preventive maintenance servicing. So, without sumps, it's a good practice to loosen the tank plug and drain off a small amount of fuel with the contaminants.
If your fleet doesn't have on-site fueling and must rely on local service stations or on-road truckstops, it's even more important to check for water/dirt in the fuel. Ask your drivers to report any fueling locations that apparently don't have in-hose filters at their fuel islands. Rather than replace a partially plugged filter, some fuel providers have been known to remove the filters to get vehicles through service islands faster.
One fleet manager interviewed found that his own people were removing filters to speed up the evening refueling rush when trucks came in. When drivers do their own refueling, they should report any "slow" pumps so filters can be replaced - not removed.
Good Maintenance Procedures
Maintenance managers should review PM procedures to make sure fuel tanks and fuel filters are serviced regularly.
Darry Stuart, a previous generl chairman of TMC, says when it comes to water in fuel, he is still a firm believer of adding a pint or more of isopropyl alcohol (rubbing alcohol) to truck fuel tanks at each PM service and more frequently during extremely cold temperatures where fuel line freeze-ups may be a problem.
Stuart now has his own business providing fleets with hands-on management leadership.
He says while there are a number of good fuel additives on the market, most of them are alcohol-based and more expensive than buying cases of isopropyl alcohol at the local drugstore. "I have never had problems with it affecting seals or O-rings, and it quickly absorbs water, emulsifying it into the fuel and carrying it to the fuel filter which, hopefully, will contain it and eliminate ice crystals from forming on filter media during sub-freezing temperatures.
"It used to be that standard OE fuel filters were adequate, but as injection pressures have gone up, and the price of injectors with it, anything but the cleanest and driest fuel is risky," Stuart says. "I personally don't think 12 - 15 micron filters are enough. About three years ago I started adding secondary fuel filters with water separators and heaters. I'm now shooting for 3- 5-micron filtration in my specs."
Alan
(Information from the December, 2010 issue of Heavy Duty Trucking Magazine) | |
|